FAST • THOROUGH • MEGASONIC HYPERCLEAN
In every industry there’s a leader. PCT’s Megasonic cleaning system is the most advanced solution for achieving HyperClean™ substrates available today. In semiconductor, MEMs, optics, LED, storage media and solar, PCT set the standard for constant-temperature baths. PCT designed the Megasonic system with a combination of moving-beam and phase-shifting technology to make it the most efficient cleaning system available — more than 90% acoustical-energy efficient. HyperClean incorporates PCT’s unique energy-transfer technology for superior submicron cleaning, reduced operating costs and high reliability. HyperClean™ incorporates PCT’s unique energy-transfer technology for superior submicron cleaning, reduced operating costs and high reliability
In every industry there’s a leader.
PCT designed the Megasonic system with a combination of moving-beam and phase-shifting technology to make it the most efficient cleaning system — more than 90% acoustical-energy efficient.
A compact, all-quartz vessel ensures superior cleanliness and high purity. The unit is stress free and operates comfortably at elevated temperatures while using fewer chemicals and saving valuable clean room space.
HyperClean™ incorporates PCT’s unique energy-transfer technology in a heated all-quartz unit for superior submicron cleaning, reduced operating costs and high reliability.
Unique Energy-Transfer Technology Improves Performance
PCT designed the HyperClean™ Megasonic Cleaning System using multiple-element
transducer arrays to create a highly uniform moving beam that constantly scans the wafers. A fixed-position array of transducers is located on the outside of the vessel, below each cassette. Energy is multiplexed from transducer to transducer. Phase shifting ensures that the energy beam is highly uniform and that dead spots are eliminated. High unit-area power densities (7 watts/cm2) are easily achieved in the liquid at relatively low power. This unique approach eliminates the need for transducer cooling present in competing systems while extending transducer life.
Multiplexing or Full-On Operation
PCT’s unique technology allows complete control of the megasonic energy used in a process. Multiplexing provides auto-switching of individual transducers for higher energy density transmission to the substrate, resulting in more efficient cleaning, etching or mass transfer. Full-on functionality allows for maximum power usage.
Easy Retrofit To Existing Wet Stations
Megasonic systems from PCT can be easily installed inexisting wet stations. Standard sizes or custom systemscan also be designed and built into your process tool, including generator only replacement with our universal
generator capability. The three different types of interfaces (RS232, digital I/O and SECS/GEM) allow for ease of integration, installation and adaptation to current facility requirements.
Features
- No moving parts for improved cleanliness
- Improved energy uniformity—no dead spots
- More than 90% acoustical-energy efficiency
- Uniform particle removal
- High-energy density with low-power output for extended transducer life
- High-purity heated quartz vessel for the highest-purity processing
- Easy to retrofit to existing wet stations
- Available for wafers up to 450 mm and beyond
- Optional filtered/recirculation version
- Acid / solvent / stripper-compatible materials available
- Available in manual and automatic stand-alone systems
- Frequency range 450 KHz – 1 MHz
Proprietary Solid-State Power Supply & Control System Offer High Reliability and Precision
PCT’s electronic control system is compact and can be located up to 12 feet (25 feet optional) from the bath. It features a
wide frequency range, auto-tuning power supply and an advanced MPU controller. An operator control panel can be placed
in a convenient location for status and control monitoring. Self-tuning smart electronics make matching transducers quick
and easy — with the push of a single button. A single control unit can run two eight-inch arrays simultaneously. The system
is equipped with RS232 and IEEE-422 ports to allow communication with host control. PCT’s unique transducer array
design provides higher energy efficiency than any other system.
PCT’s Megasonic Cleaning System Options
• Transducer plates
• Custom transducer assemblies
• Quartz, stainless steel, or plastic tank materials
• QDR, recirculating or static
• Clean, rinse or resist strip applications
PCT Certifications
• ETL File No. 567511 per UL 3101-1
and CSA 1010.1
• CE EN 61010-1 European Safety Approval
• CE EN 55011 European EMI Approval
• CE EN 50082-2 European ESD, RF, and Transient
Susceptibility Approval
Specifications
Operating Frequency | 600 kHz to 1 MHz at resonant levels |
Operating Temperature | 20° – 70° C |
Power Requirements | 200 – 230Vac 50/60 Hz Single phase, 10 amps for ambient temperature operation Optional single phase, 30 amps for elevated temperature operation |
Materials of Construction | |
Tank | Quartz, Stainless Steel, Plastic or FM4910 compliant material |
CERTIFICATIONS

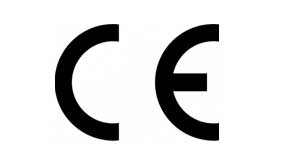
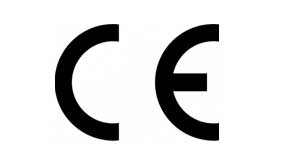
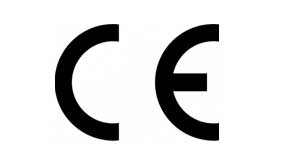